Traceability is more than just a “buzz word” in manufacturing. It has become a necessity in order to provide suppliers with the data they need to ensure their Product has been created as designed, with the quality and the accuracy of their material and processes validated.
Having the ability to not only harness your data but also to utilize it in analysis is invaluable. This data can provide you numerous opportunities for continuous improvement, cost savings, improved efficiencies, etc. Think of your data as the forensic proof that your product is produced as expected and to spec each and every time.
A solid Manufacturing Execution System (MES) can not only provide you with this data, but the peace of mind that your facility is executing best practices and producing solid quality products. Having the ability to capture defects at the point of failure and product recall control are huge assets when you consider the ROI for an MES system. The options and possibilities for any manufacturing organization are endless.
In this paper you will understand more about:
- What is Traceability?
- Why is Traceability Important?
- How has Traceability Evolved?
- What is an MES?
- Why would my organization need an MES?
- Component Traceability
- Traceability Protecting your Brand
Happy Learning! Now let’s get started.
What is Traceability in Manufacturing?
Simply put, traceability in manufacturing is a combination of the content record and process history of any given product, combined with the ability to then act on that information.
There’s a lot of talk currently around the idea of a digital twin, a common reference to the digital representation of a product specification or design. Traceability takes that digital twin concept to another level and builds an exact record of each piece or batch produced – including actual measurements, content, and specifications. It then utilizes that information to make sure that the producer is making the right parts, the right way, at the right time.
What Makes Traceability so Important?
Using traceability in manufacturing is important to maintain and gain a competitive advantage. How does traceability do that? Through cost reduction, improved customer scorecards, responsiveness to market conditions, delivery of value-adds, and brand protection.
A well planned traceability system leads to increased piece part and batch quality. When you increase quality, you’re reducing rejected production and rework, reducing scrap, and increasing yield, which directly impacts cost. Ancillary costs like expedited freight or machine downtime are also improved through the use of traceability systems. Traceability is also used to optimize order processing and minimize inventory buildup so that you’re making the right parts at the right time. Higher inventory turns, better work in process inventory visibility, and precise execution-to-order yields higher efficiency and lower costs.
The highest occurrences of negative customer scorecard entries can be mitigated by using a traceability system. Issues like on time delivery, proper labeling and identification, order fulfillment accuracy, and product quality are managed and controlled with a traceability system. Once the precise facts are known about the products being made and the processes which they go through, those facts can be utilized to make sure the right parts are being made the right way at the right time.
Traceability will also help with the mitigation of liability and recall exposure. Rather than dealing with statistical population methods to estimate the impact of a product issue, traceability allows you to identify the exact products which may be suspect, and narrow the exposure exponentially. This allows you to quickly identify products by serial number or by lot that might be subject to the same conditions and recall very limited quantities to address those issues. Smaller recalls lead to lower costs and higher brand impression.
How Traceability Has Evolved
These days, as materials arrive at the manufacturing facility they’re identified, validated against orders, validated against accepted lot numbers, and validated against vendor inspection protocols. Inbound products that require further inspection are then routed to inspection areas. If no further inspection is required, then they’re routed to an inventory store or directly to the production line.
As those materials make their way to the line for use in production, they are typically either barcode scanned or RFID scanned and validated at the point they enter the line to make sure that the right parts are used for what is being built at the time.
This level of sophistication and automation wasn’t always the case, though. In fact, in recent years, traceability has evolved in three key areas:
1. Interoperability
Business systems are more interconnected to traceability systems and traceability systems are more interconnected to the industrial controls. Data is more connected to the product life cycle management systems, so now you have a more cohesive ecosystem from design, build, and post-build analysis.
2. Performance Dashboards
The introduction of performance dashboards has allowed plant management to view in real time the performance of their manufacturing facility. They can hone in on specific lines or even specific stations so that any bottlenecks can be quickly identified and addressed.
3. Data
The proliferation of data with systems becoming much faster and storage becoming much cheaper has changed everything. The amount of processed data together with real evidence – video, photo, or logs – now provides the ability to get a much more accurate digital twin in place.
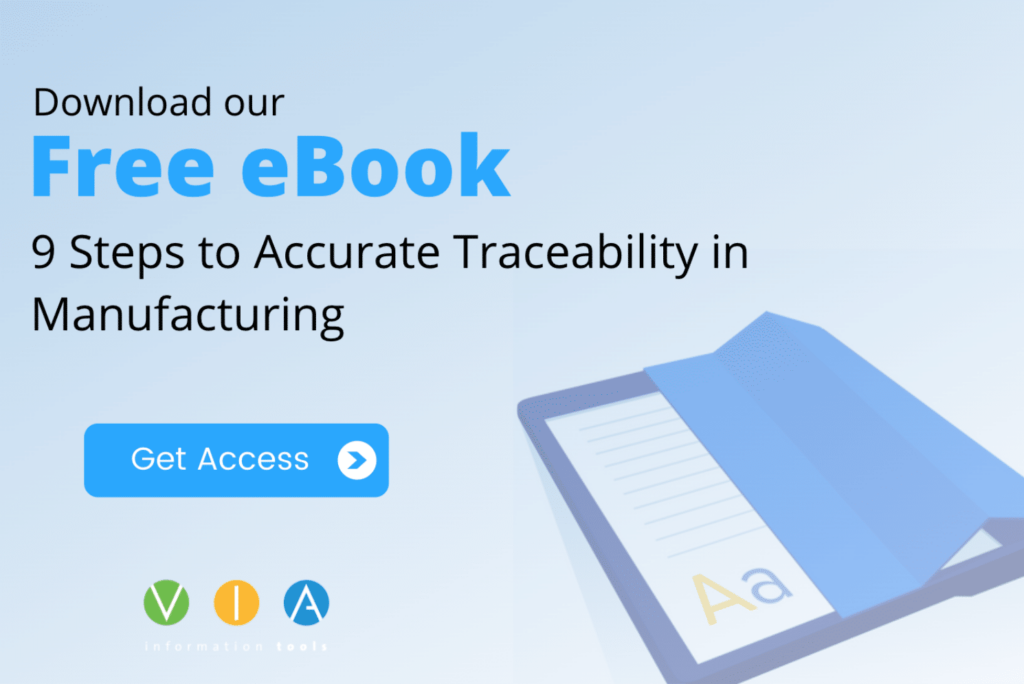
What is Manufacturing Execution Software (MES)?
Manufacturing Execution Software, or MES, provides a computerized tool to enforce, track, and record data related to manufacturing processes. In today’s world, it’s an absolutely essential tool for making sure that your production environment is operating at maximum efficiency.
The best MES solutions offer granular genealogy data about the entire manufacturing build process from the incoming raw materials to the outgoing finished goods. Certain features, like Bill of Materials and Routing Enforcement, ensure that your products are being built as designed while at the same time capturing the data to guide analytics and the decision-making process.
This level of data, or traceability, can empower you and your team to make informed decisions in real-time that analyze trends, solve problems, and move the business forward..
[DOWNLOAD] 9 Steps to Accurate Traceability in Manufacturing
Manufacturing is all about consistency, and a good MES will guide your workforce with the consistency and standardization that delivers results.
Here’s how it works:
MES provides real-time data to capture defects as they occur at the point of failure. The error-proofing layer will ensure that the parts recipe – or Bill of Materials – is followed as well as the route the part must take in order to be a completed assembly.
As a leader in your manufacturing environment, having that peace of mind that your shop floor has a tool that helps eliminate human errors and reduces waste is invaluable. You’ll be able to understand everything that affects your production so you can:
- Reduce scrap
- Understand why you are getting scrap
- Increase visibility to downtime
- Understand the reasons for downtime
- Better tooling
- Greater machine efficiency
- Greater employee efficiency
- Continuous improvement
Manufacturing Mistakes to Avoid
If you aren’t using MES in your plant, you’re risking having little to no visibility into your shop floor and no data from which to draw important insights.
For example, the lack of defect containment at the point of failure can unleash lasting damage on your brand reputation, not to mention the financial fallout that can come from a product recall.
Without real-time data from employees, machines, and tooling to understand your efficiency levels, your management’s ability to make informed decisions that guide the business is severely reduced.
MES vs ERP
Many people use the terms MES and ERP interchangeably, but they are in fact distinctly different. Yes, these systems should work seamlessly together. However, one should not be confused with the other. An MES or Manufacturing Execution System, should provide real time data and as the name states provide the execution tool and validations to guide your shop floor systems, machines and processes. Whereas an ERP, or Enterprise Resource Management System, is for organizations to manage daily business activities such as accounting, procurement and supply chain management.
An MES should integrate with your ERP as well as your shop floor equipment and operations. These systems should work together to provide an accurate picture of your manufacturing environment. The data an MES provides to your ERP ensures that your inventory, planning and purchasing decisions are made with the most accurate data possible.
If run properly, an MES should handle your shop floor’s execution, shop floor connectivity, and necessary error-proofing validations while providing real-time production data. An MES can also save you money. When you have the ability to identify problem areas and ensure that you are only shipping good parts that are identified properly, then the cost spent on expedited shipments because of manufacturing issues or misidentification is no longer at the top of your issues list.
What is a Components Traceability System?
A components traceability system provides the capability, and enforcement, of scanning items and linking them to assemblies or batches of assemblies. That’s typically done with a unique ID or a barcode on each item and package.
This provides the manufacturers with the ability to track and trace the component vendor, lot information, and collect process information tied to the parts in the system. It also allows manufacturers to see what’s produced through each operation and what customers the items were potentially shipped to by tracing the components. Plus, the ability to track and control inventory and monitor and evaluate scrap and waste.
Do I Need a Components Traceability System?
Yes, most manufacturing can benefit from this in one way, shape, or form.
For example, most of our customer base is automotive and they have a variety of components that need to be identified, barcoded, or have a serial number etched on them.
The same goes for our electronics customers with the electronic boards that go into products, like imaging equipment, and need to make sure that they’re scanning the right board for top-level assembly.
An additional functionality from the components traceability is that it provides a method for them to do the electronic quality tests, collect the values, and tie them to the components before they ship them.
So, if the worst happens and they’re faced with a product recall, they have the historical data of which products where – and when – who did it, and when it was shipped. They’re also able to see which quality tests and inspections were passed along the way.
We also have one food-based customer that uses components traceability for a process as simple as processing chicken into chicken nuggets. There’s data behind the whole process, including FDA compliance, so they have the data to show that they are processing food safely and according to regulations.
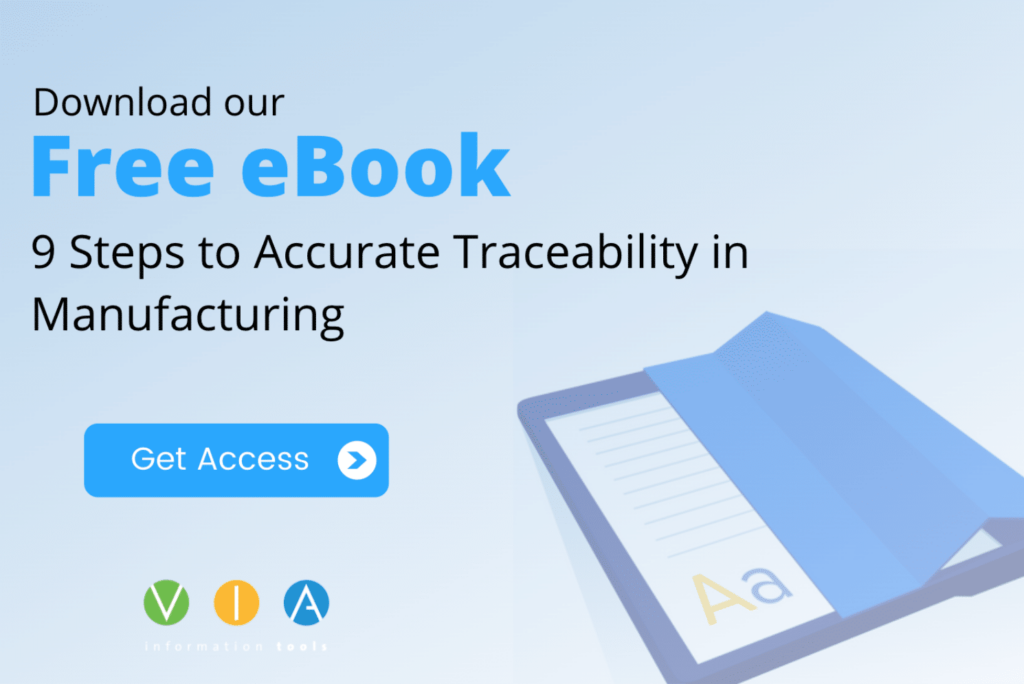
How Components Traceability Protects Your Brand
Without the real-time insights and historical data that components traceability provides, you’re at risk of product recalls, and possibly violating federal regulations pending the requirements of your product..
If you produced 5 million bad widgets that get shipped and delivered all over the world and then you need to issue a product recall, that can be devastating for your business. Not only is that extremely costly to execute, but the damage to your brand can be irreparable. If the story gets in the news or on social media – which we have all seen examples of – well, that’s pretty much a nightmare scenario for manufacturers.
You might be tracking some data through spreadsheets or some clunky pen-and-paper system scattered around the office, but it’s a highly manual process and prone to human error.
However, with a components traceability system in place, all of that historical data will be 100% accurate, easily accessible, and able to provide meaningful, actionable insight.
Getting Started With a Components Traceability System
Are there any federally-mandated requirements required for your products? If so, you could probably use a lot traceability system. Don’t waste time and energy sorting through data papers, spreadsheets, and clipboard checklists to collect that data.
If you’re having trouble managing inventory, or issues with your supply chain, you could probably use a traceability system.
Grab some time with our team of experts and take the first steps today!