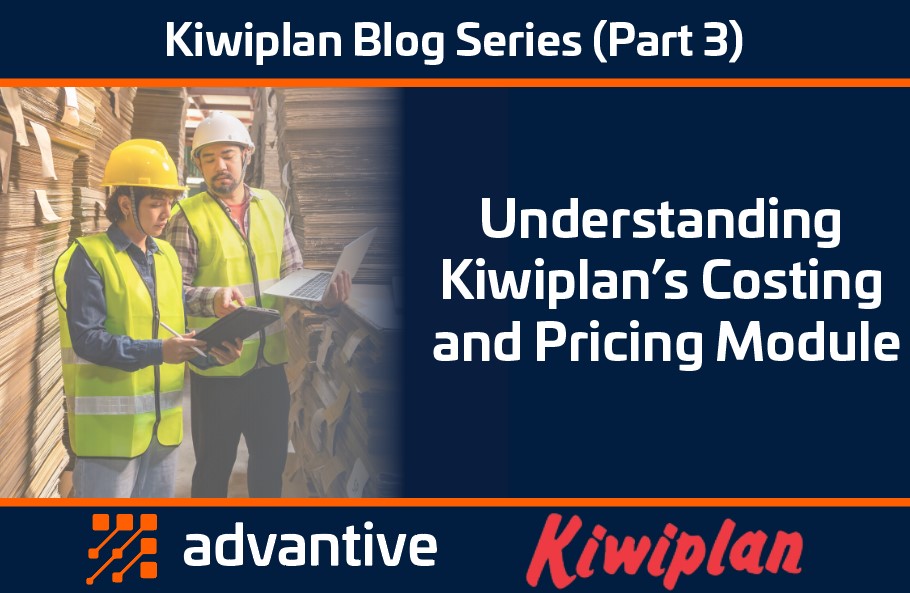
Welcome to part 3 of the Kiwiplan blog series! Last time, we explored Kiwiplan’s order management module, covering the home screen, watch lists, quoting, order entry, and more. This week, we’re shifting our focus to one of the most crucial aspects of any manufacturing and business operation: Costing & Pricing.
Let’s Take a Look at Costing & Pricing in Kiwiplan
The Kiwiplan Costing and Pricing module helps packaging manufacturers with the crucial exercise of determining how much to produce and sell. Kiwiplan enables our customers to estimate costs and set prices accurately. Up to this point, we’ve discussed creating a quote, building a product design, and placing an order. Now, we’re going to address the big question: “How much is it going to cost?”
Different Types of Pricing
Kiwiplan offers various pricing strategies, typically involving a markup on cost per MSCs. Sometimes, pricing is margin-driven and reflects the actual market conditions. It’s crucial to perform both pre-production and post-production costing to understand variances between estimated and actual costs. Kiwiplan’s variance reporting feature can help you identify errors in estimates and highlight where costs were lower or higher than expected.
Pre-Production & Post-Production Costing
Kiwiplan’s pre- and post-production costing features are rule-driven, using straightforward “if, then, else” logic. This simple form of coding allows for easy adjustments to the costing algorithm. You can double-click the number to see the detailed calculations for an item’s cost, which provides transparency in cost derivation. With our costing feature, you will always know how costs are calculated to enhance your decision-making process.
Why Are Machine Rates, Setup, & Waste Important?
Costing and pricing are directly influenced by machine rates. When estimating costs, you need to account for labor, materials and freight costs. Indirect costs like power, admin salaries, and warehouse expenses also play a role. However, most cost components specifically relate to the speed, setup time, and waste associated with the machinery on the plant floor.
Kiwiplan uses “Degrade Rules” to manage this information. Materials and freight costs tend to be straightforward, but labor costs can vary based on several factors, such as set rates, machine hours, and task-specific labor hours. This feature adjusts machine speeds from the fastest possible to those determined by job characteristics. It also allows you to have an unlimited number of characteristics change the speed of the machinery. You can use any field in the database or user definable fields to adjust the machine rates.
Additionally, you can do costing and routing by using different rules. For example, you might use a specific rule for cost estimates and another for determining how quickly a machine will run on the factory floor. The same applies to waste, setup waste, and run waste. You can use the history from your production to help generate and change the costing rules, as well as come up with plan speeds, plan setup times, and waste characteristics.
What’s Coming Up?
Today, we discussed Kiwiplan’s Costing and Pricing module, including the different types of pricing, pre- and post-production costing, and machine speed, setup, and waste. This module concludes what we consider to be the front end. Next week, we’ll discuss our Purchasing module which encompasses sheet ordering and purchasing items needed to manufacture a job. Stay tuned for the next installment in our blog series!